无烟高压空气辅助系统(HPAS)
In order to meet increasingly strict environmental regulations and to promote cleaner energy at their facilities, many oil, gas, and petrochemical companies are seeking to upgrade existing flares to allow smokeless flaring of hydrocarbon gases. The main areas of application for these flare upgrades are located in Africa, Middle East, South America, and other countries with high oil production capabilities and programs. Many of these areas have utility flares located in facilities where a shortage of steam or water prevents conventional smokeless steam-injection systems from being added. Mr. Mazen Mashour of Saudi Arabian Oil Company has patented a new smokeless flaring technology using high-pressure air. This technology is called High Pressure Air Assist System (HPAAS) and has been successfully implemented on dozens of flare systems in Saudi Arabia. It uses supersonic air injection nozzles to inspirate smokeless air at a much higher efficiency than any previous smokeless high-pressure air-assisted flare technology. This has resulted in a system that can be easily retrofitted to existing flare systems in a quick and cost-effective manner. The technology will soon be used at facilities worldwide to create cleaner, more environmentally friendly flare systems. This paper describes the advantages of HPAAS over conventional systems, and also discusses the approach used in developing the technology.
BACKGROUND
Saudi Aramco is the largest oil company in the world and has hundreds of flare systems located at their various upstream and downstream facilities. The company’s largest concentrations of flares are at the Gas Oil Separation Plants (GOSP) and the corresponding production fields near these locations. Most of the flares at these locations were installed during the past 50 years using utility flare non-smokeless technology and were designed using older API RP-521 guidelines that recommended maximum exit velocities of 0.20 or 0.50 Mach, which results in a large diameter flare tip, often 48”to 84” in diameter [1]. In addition, the available inlet pressures are very low and large diameter tips are required to meet the allowable pressure drop. The continuous operating conditions for these flares are often low flowrates composed of purge gas, control valve leakage, or tank vapors. This mixture of gas exits at a low velocity and smokes continuously.
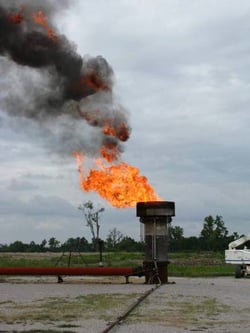
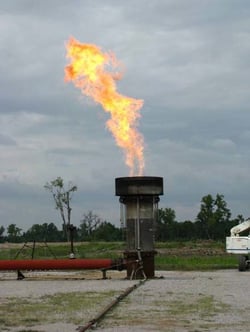
CONCLUSION
At the time this paper was written, approximately fifteen (15) of the GOSP locations on the Southern Area Smokeless Upgrade Project had been successfully retrofitted with the HPAAS flare systems. According to the current schedule, the remaining GOSP’s will be retrofitted before the end of 2009. All of the installed HPAAS tips have provided the same smokeless, low-radiation performance that was desired. The project has been a great success for all parties involved.
下载技术文件