新一代低氮氧化物锅炉燃烧器改造-现场性能和考虑因素
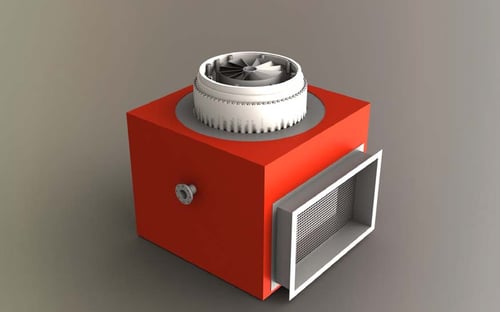
In 2006, the Valero Corpus Christi Texas Refining facility purchased Zeeco® GLSF Free-Jet Next Generation Ultra-Low NOx Burners for two boilers in order to comply with emissions regulations. These boilers were identical in design and operating conditions. The GLSF Free-Jet burner provided the most economical option for meeting the emissions regulations, as they do not require External Flue Gas Recirculation (EFGR). Each boiler is over 70 years old, and retrofitting ultra-low emissions burners without using EFGR to meet strict emissions requirements was challenging.
Abstract
Burner retrofits in industrial boilers are an economical solution to achieving lower NOx levels with existing fired equipment. However, designing a next generation ultra-low NOx burner footprint that fits into an existing burner cutout continues to be an industry challenge in many applications. Building a burner with a flame pattern or profile that can operate properly within the existing space and back wall firing length limitations while still achieving significant NOx reductions has also proven to be a difficult task.
Zeeco has developed a patented next generation ultra-low NOx free-jet burner technology with a compact mechanical footprint. The GLSF Free-Jet Burner produces a flame profile with very limited flame-to-flame interaction for multiple boiler burner installations, while also achieving shorter flame lengths.
One of the other primary concerns for the end user operating company is the overall cost of ownership for next generation ultra-low NOx burners. They can have higher maintenance costs versus conventional emission boiler burners. Zeeco provides the lowest maintenance design on the market for similar NOx emissions results. We will review these design details, specific retrofit installation details and lessons learned during a retrofit of existing boiler burners at Valero’s Corpus Christi Refinery in this paper, including tramp air impact, and field emission test results for several of the retrofit applications.
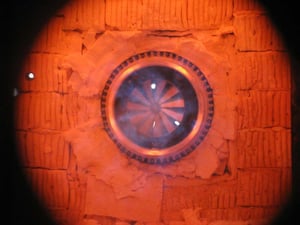
Original Design Conditions
Each boiler was equipped with two conventional burners. Information on the boilers was limited due to age of the installation, and many of the details in regards to next generation burner retrofits were not important 70 years ago and were therefore not clearly documented. Additionally, some original design documentation was missing. Zeeco replaced each of the existing conventional burners with a Zeeco GLSF Free-Jet burner. The heat release design of the new burners was set at 77.4 MM Btu/hr per burner. The combustion air pressure drop was set at 3.25” W.C. at 15% excess air with an air temperature of 100° F.
The new burners were designed to use 0.3 lb steam/lb fuel gas injected into the fuel gas stream for increased NOx reduction if needed since EFGR was not planned for this application. The use of a small amount of steam was less expensive than reworking the boiler to add approximately 14% EFGR to achieve the required NOx emissions level of 0.03 lb/MM Btu (HHV).
The new burners were installed in the existing burner wind-box configuration. The new burner footprint was approximately the same size as the existing burners, so boiler modifications for burner installation were minimized to reduce the overall installation cost of the retrofit.
总结
The retrofit of the boilers was very challenging due to the age of the boilers and the amount of information available for the application. However, after the challenges were identified and addressed, the boilers were able to achieve the required 0.03 lb/MM Btu NOx emissions and 50 ppmv CO emissions without the use of EFGR. Using Free-Jet mixing technology with flame stabilization ledges and careful field assessments and adjustments reduced the initial retrofit costs and the long-term maintenance and operation costs.
下载技术文件