低排放 - 低维护燃烧器设计
In order to meet the ever increasing and strict emission controls on fired equipment, low emission burner retrofits are becoming commonplace. In the past, burner design has focused primarily on achieving emission requirements, almost at the exclusion of future burner maintenance requirements. With so much design focus on meeting emission requirements and none on future burner maintenance requirements, operators struggle with burners that may have met emission targets when initially installed, but quickly became a maintenance burden in order to consistently achieve the required emission levels.
By combining end user field feedback with an understanding of factors that lead to continued burner field maintenance, this paper will demonstrate how low maintenance burner design features can be integrated with low emission burner design requirements and still meet emissions targets. The Zeeco patented next generation FreejetTM burner incorporates these low maintenance features.
This paper will review specific low maintenance design features that should be incorporated into the burner design. These features include:
- Review of gas tip design via Computational Fluid Dynamics (CFD)
- Gas tip port selection
- Gas riser review
- Combustion air control mechanism
- Burner tile block
Burner Maintenance (or lack thereof) Impact - Issues, Causes, Remedies
Burner maintenance can be driven by many factors. Emission control typically has not been one of the factors until recently. An absence of or a lack of focus on proper burner maintenance can result in several undesired results that include:
a) Burner Instability – Flames lifting off the burner and lighting intermittently. This creates a safety hazard for operation personnel attempting to adjust the burners via potential flame blowback, or in the worse case, a heater explosion where some of the burners are lit, others have gone out and the firebox fills with unburned fuel gas that ignites explosively, damaging the heater and creating safety hazard for the plant personnel.
b) Flame Quality – Flames that are not developing in a controlled defined shape and can be damaging to the process tubes via flame impingement. Poor flame quality can cause warping of the heater floor causing damage to the refractory floor, burner tiles, or heater steel. If the flame quality is sufficiently poor it can also limit the heater throughput via flame impingent on the process tubes leading to coking of the product inside the tubes.
c) Unsustainable or Higher than Allowable Emissions – In the past, maintenance was driven by a desire to reduce mechanical damage to the heater, flame impingement on tubes that could reduce heater throughput, or safety driven concerns. Now, achieving sustainable emission levels is also required. Continuous Emission Monitors (CEM’s) are now placed on many units to continuously measure and report heater flue gas emissions. Prior to CEM’s, many heaters were tuned for the annual emission verification test with little preventative maintenance until it was time to achieve the desired emission rates again the following year.
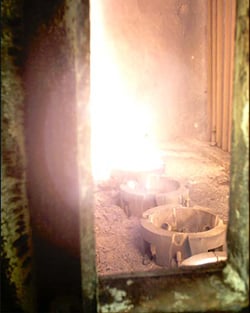
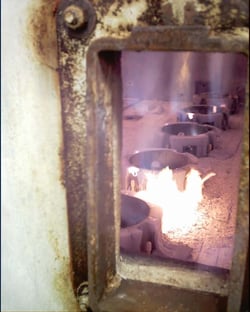
总结
Incorporating low maintenance design features into the initial burner design will lower the cost of burner maintenance and result in sustainable emission control.
These burner design features include:
- Eliminate metal in the burner throat
- Keep gas tips and risers from radiant firebox exposure
- Keep gas risers out of preheated combustion air stream
- Utilize low metal mass gas tip
- Eliminate small stability / ignition ports and maximize port area in the gas tip
- Design burners for high turndown to eliminate shutting in of gas tips
- Supply single piece burner tile
- Gear driven sealed bearing air damper adjustment