乙烯裂解炉中的燃烧器应用
This abstract will focus on the field results of eight ethylene cracking furnaces which use Zeeco GLSF Enhanced Jet burners at PetroChina Sichuan Petrochemical Company Limited (SPC) which achieve field measured NOx emissions significantly less than 90 mg/Nm3. Zeeco has found that using ultra low emissions burners in ethylene cracking applications is prove an economical solution for achieving NOx levels lower than 90 mg/Nm3 from existing fired equipment. Providing a next generation low NOx burner footprint that fits into ethylene cracking applications can be challenging in many applications. Ultralow NOx burner flame pattern(s) or profile(s) that can operate properly within the required burner-to-burner spacing and heat flux limitations has also proven to be a challenge.
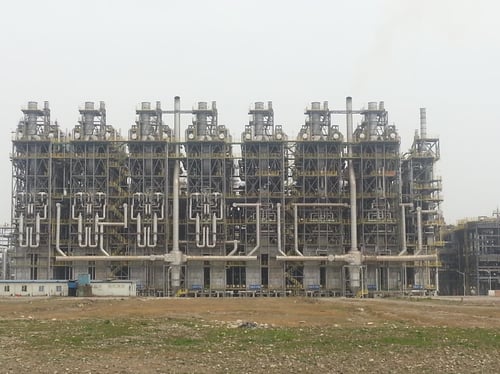
This paper will focus on an application using the GLSF Enhanced Jet Flat Flame Burner model where NOx emissions averaged around 50 mg/Nm3 in the field. The furnace field measured NOx emissions ranged between 35 mg/Nm3 (17 ppmv) to 65 mg/Nm3 (32 ppmv) at designed heat release. The GLSF Enhanced Jet floor burners utilize the basic “free-jet” method of mixing fuel gas and inert products of combustion to form a new combustible mixture before entering the combustion air stream. The resulting mixture burns at a lower adiabatic flame temperature, resulting in lower thermal NOx production.
Zeeco developed this ultra low NOx emissions burner technology to provide a very small mechanical footprint and excellent heat flux profile without flame-to-flame interaction or flame rollover. Flame interaction between burners can cause flame impingement upon the process tubes and increased emissions. Flame impingement can result in shorter run lengths and higher tube metal temperatures, problematic issues in prolonged ethylene production.
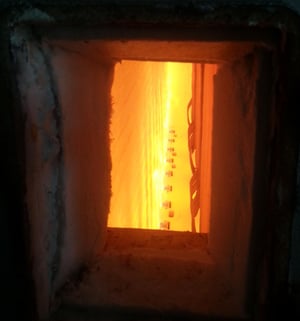
Comparison to Low Emissions Burners
Ultralow emission burners found in ethylene cracking units typically utilize a type of staged fuel technology with a large portion of the gas ejected from the staged gas tips. These particular burners have staged fuel tips strategically positioned for fuel to exit the orifices and pass over the combustion air stream before reaching the wall. (See Figure 3, “Low Emission Staged Fuel Burner”) To modify the flame pattern and achieve an even heat flux in the lower portions of the flame envelope, the orifices must be drilled at increasingly abrupt angles toward the furnace wall. These orifice angles cause the air and fuel gas to mix at a faster rate, thus increasing thermal NOx, and requiring a compromise between the heat flux profile and thermal NOx production. As the heat flux profile is made more uniform, with an average above 90%, the NOx emissions typically increase along with the increase in flux percentage. In the same respect, as the NOx is decreased, the heat flux percentage is also decreased.
The location of the staged gas tips also affects the flame quality of the burner. For example, if the burner is required to make very low NOx emissions, the staged orifices must be aimed in a more vertical direction. This vertical direction, coupled with the combustion air stream located in between the unburned gas and the furnace wall, increases the likelihood of flame impingement. The mixing of the fuel gas energy becomes so reduced at higher elevations that the furnace currents can easily influence the flame toward the tubes. In general, the lower the NOx emissions when staged gas passes completely over the combustion air opening, the higher the tendency for flame impingement or hot spots on the tubes.
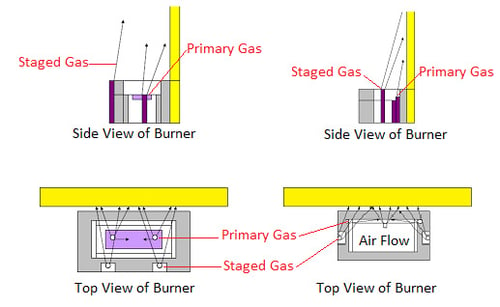
总结
This project showed eight ethylene cracking furnaces with Zeeco GLSF Enhanced Jet Burners achieving challenging emissions requirements of less than 90 mg/Nm3 NOx emissions. Even though the burners were mounted closely together, they showed no signs of flame interaction or flame rollover. The compact burner design allowed more burners to be installed closer together without adversely affecting flame behavior. The GLSF Min-Emissions & Enhanced Jet burner designs have been used in more than 340 challenging ethylene cracking furnaces, including those requiring NOx emissions guarantees of less than 90 mg/Nm3. The GLSF Enhanced Jet burners used for this application achieved field-measured NOx emissions between 35 mg/Nm3 (17 ppmv) to 65 mg/Nm3 (32 ppmv) at designed heat release.
下载技术文件