蒸汽辅助火炬的可接受操作参数
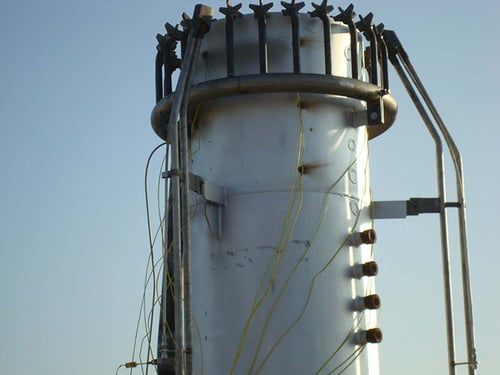
Flare vendors recommend that cooling steam should always be supplied to the steam injection equipment on steam assisted flare tips. However, the nomenclature of “cooling steam” properly describes only one aspect of this steam flow. Not only does this steam provide thermal protection to the steam injection equipment in the high-heat zone near the tip exit, but this steam flow also ensures the steam supply piping remains heated, preventing condensate formation during large increases in steam flow rates. Unfortunately, during periods of low gas flow rate to the flare system (standby, purge-only, or small continuous flow rate modes) this cooling steam can reduce the hydrocarbon destruction efficiency of the flare system.
Currently the Texas Commission on Environmental Quality (TCEQ) is reviewing data from flare testing they commissioned through the University of Texas in 2010. Recent field observations by TCEQ have revealed what appears to be poor flare destruction efficiency by some steam and air assisted flares when operating at turndown condition. Using specialized infrared cameras, unburned hydrocarbons were detected coming from improperly operated flare systems. Despite these findings, the general belief amongst industry flare experts is that through proper operation of existing flares, the destruction efficiency can be very high even at turndown rates. However, meeting proper destruction efficiency requirements with existing flare systems at low gas flow rates will require more clear and detailed training for operations personnel at these facilities.
Objective
The primary objective of the Zeeco steam flare research was to test current Zeeco steam assisted flare tip designs for destruction and removal efficiency of hydrocarbons while firing at American Petroleum Institute (API) 521 recommended purge gas rates with steam injected at Zeeco’s recommended cooling steam rates. A secondary goal was to develop a relationship between the flare tip design, the combined steam and purge gas lower heating value (LHV), and the hydrocarbon destruction and removal efficiency.
Testing
Testing began on July 18, 2011, and spanned a period of five days. Ambient condition measurements were taken by Air Hygiene before testing began to be used as a control for background readings of carbon levels in the facility.
Testing occurred in three phases.
Phase 1: Testing Established Guidelines
Phase 2: Adjusting Test Plan and Building Hypothesis
Phase 3: Verifying LHV Hypothesis
Results and Conclusions
Zeeco has learned that while constant steam injection (cooling steam) provides thermal protection to steam injection equipment, improper steam injection can create downsides. Though steam is an integral part of maintaining the integrity of flare components, improper use can become an impediment to the destruction and removal efficiency of hydrocarbons. Many factors must be considered when utilizing steam for combustion. From this research, Zeeco now believes adequate combustion is not possible when using API 521 specified purge gas and current steam cooling rates
下载技术文件