无烟空气辅助和火炬气体回收技术的持续火炬管理
Flares are an important safety feature of most oil and gas producing and processing facilities, providing a safe and effective means for burning waste gases during a plant emergency. These emergency conditions often coincide with power outages, loss of steam, fire in the plant, or a variety of other scenarios. Flares are also used to safely burn any continuous relief cases that can result from on‐going processes, control valve leakage, purge, etc. In recent years, local governments, air quality agencies, environmental groups, and end users have pushed to reduce the amount of continuous flaring. These particular flaring cases are viewed as wasteful, polluting, and potentially hazardous to humans. This paper will discuss several different methods for reducing and/or mitigating the impact of continuous flaring as part of a Flare Impact Mitigation Plan (FIMP).
In an FIMP, one of the first steps should be to better understand the continuous flaring sources in a facility. This can be a challenging process, as the local operators may have a tendency to underestimate the amount of continuous flaring that occurs at a facility. A realistic estimate of the flaring must be obtained in order to determine the best and most economical course of action. Flares are an important safety feature of most oil and gas producing and processing facilities, providing a safe and effective means for burning waste gases during a plant emergency. These emergency conditions often coincide with power outages, loss of steam, fire in the plant, or a variety of other scenarios. Flares are also used to safely burn any continuous relief cases that can result from on‐going processes, control valve leakage, purge, etc. In recent years, local governments, air quality agencies, environmental groups, and end users have pushed to reduce the amount of continuous flaring. These particular flaring cases are viewed as wasteful, polluting, and potentially hazardous to humans. This paper will discuss several different methods for reducing and/or mitigating the impact of continuous flaring as part of a Flare Impact Mitigation Plan (FIMP). In an FIMP, one of the first steps should be to better understand the continuous flaring sources in a facility. This can be a challenging process, as the local operators may have a tendency to underestimate the amount of continuous flaring that occurs at a facility. A realistic estimate of the flaring must be obtained in order to determine the best and most economical course of action.
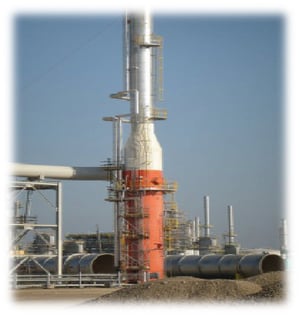
Some facilities have flare gas thermal mass or ultrasonic‐type flowmeters installed in the flare lines that measure and record flare gas flowrates on a continuous basis. Each type of flowmeter has a limited turndown capability, so it can be difficult to obtain accurate flowrate readings in large flare headers (36” and larger).The flowrate should be averaged over a period of several weeks or months to capture both emergency and continuous flaring conditions. The operation of the facility should also be evaluated to determine if there are any regular or planned maintenance scenarios that occur on a frequent enough basis to be considered normal conditions.
After collecting the data, each facility (or end user) should make their own determination of what flowrate is considered the normal, continuous rate and what flowrate is considered emergency flaring. Local regulations may only allow a certain number of hours of emergency flaring within a 24‐hour period. Location of the facility should also be evaluated. If the plant is located in a remote area, then flaring events may not affect local communities. A preferred solution in these particular cases is to upgrade the flare to ensure that the continuous rates operate without producing any visible smoke. However, if the facility is in close vicinity to urban areas, it may be necessary to completely eliminate any continuous flaring due to public concern. Some facilities have flare gas thermal mass or ultrasonic‐type flowmeters installed in the flare lines that measure and record flare gas flowrates on a continuous basis. Each type of flowmeter has a limited turndown capability, so it can be difficult to obtain accurate flowrate readings in large flare headers (36” and larger).The flowrate should be averaged over a period of several weeks or months to capture both emergency and continuous flaring conditions. The operation of the facility should also be evaluated to determine if there are any regular or planned maintenance scenarios that occur on a frequent enough basis to be considered normal conditions. After collecting the data, each facility (or end user) should make their own determination of what flowrate is considered the normal, continuous rate and what flowrate is considered emergency flaring. Local regulations may only allow a certain number of hours of emergency flaring within a 24‐hour period. Location of the facility should also be evaluated. If the plant is located in a remote area, then flaring events may not affect local communities. A preferred solution in these particular cases is to upgrade the flare to ensure that the continuous rates operate without producing any visible smoke. However, if the facility is in close vicinity to urban areas, it may be necessary to completely eliminate any continuous flaring due to public concern.
总结
Flares play an important safety role at a facility, providing a safe and effective means for burning waste gases during emergency conditions. However, when continuous flaring is required, there is a preference for flaring to be mitigated or eliminated. The proper solution for this change should be determined as part of a Flare Impact Mitigation Plan (FIMP). Two different types of solutions were discussed as a result of an end user’s FIMP. The first is upgrading their GOSP facilities with HPAAS smokeless flare technology. The second is adding FGRU systems to some of the larger facilities. Both of these solutions provide an attractive method for reducing the negative impacts of flaring. The energy industry is continuing to move forward with more effective solutions, such as Flare Gas Recovery. Zeeco is an experienced Flare and FGRU supplier, and can provide a variety of assistance for customers requiring economical and effective solutions.
下载技术文件