燃烧乙烯的先进火炬头的环境测试火炬
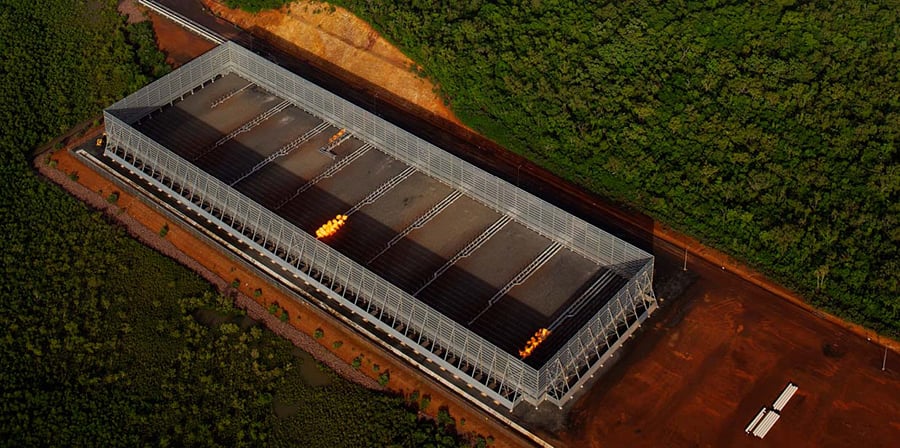
As part of the development of a new advanced flare tip for a Low-profile flare field, several experiments have been conducted to establish the flame height/shape, the smokeless performance, and the radiant flux profile for wind and no-wind conditions. Zeeco’s flare test facilities have the ability to fire single and multiple tips to evaluate burner spacing, firing rates, fuel types, and radiation flux for a specific flare tip design. Work performed in the current testing included a single burner test with two different tip designs and a three-burner test with the same tip design. These results show flame heights and shapes as expected. Radiant fluxes from the single and threeburner tests also perform as expected. Data from these tests were used to help validate CFD predictions performed for these tests and applied to a full flare field calculation.
INTRODUCTION
In 2006, Zeeco received a contract from a major chemical company to design and supply a large multipoint ground flare system for a major grass roots olefins facility in the Middle East. The process requirements for this facility are very strict, and in general, outside the normal range of constraints and process requirements that are applied to multipoint ground flare systems for such plants. Zeeco agreed to supply the system and meet the performance and testing and modeling requirements that were defined in the customer’s specifications. This included full scale firing of three (3) burner tips.
BACKGROUND ON MULTIPOINT FLARES
Multipoint staged ground flare systems have been used in the refining and petrochemical and production industries since they were first conceived in the early 1970’s. The overall concept of these systems is to spread the combustion over a large area to facilitate air access. These systems were first used in the Middle East, and other major oil production areas as Candle Flares.
The original systems were very simple, a horizontal pipe manifold with multiple vertical pipes that were used as burners. These original systems had no staging and did not have defined burner tips. Ignition was difficult, there was little flame stability, and the systems would smoke. The original goals were to somewhat improve combustion, and to lower the major combustion closer to grade, which was generally accomplished. Note all of these original systems were burning produced gas, which consisted of moderate molecular weight mixtures of saturated gas components.
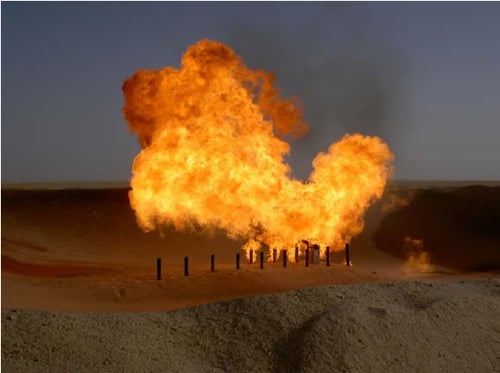
RESULTS
The end results of the testing was the development of a burner tip assembly that could achieve the smokeless burning required by the customer for the wide range of gases for the flare system, while still meeting the noise level and flame height constraints. The final burner layout in the flare field was confirmed using CFD modeling for air access and flame length. Figures 7 and 8 show testing of the final burner design at the maximum test pressure of 0.80 kg/cm2.
下载技术文件